Factories of the future - What will manufacturing facilities look like in 2044
The year is 2044. The streets of our cities are paved with electric chargers and the faint buzz of drones making deliveries fills the air. AI and robotics have reshaped the relationship between humankind and machine, but what do the factories of the future look like? Here Erez Tsur, CEO and co-founder at AI start-up QualiSense describes what factories will look like 20 years in the future.
The landscape of manufacturing is set to evolve dramatically over the next two decades, as cutting-edge technologies redefine the way we produce goods. To envision what the future may look like, we do not need to rely solely on idle speculation. Instead, by looking at some of the cutting-edge technologies that are already being pioneered by innovators today, we can extrapolate from this to see what may be commonplace by 2044. Here are five key technological trends that will reshape the manufacturing space over the next two decades:
Collaborative robots
We are already entering the era of collaborative robots. Unlike traditional industrial robots that are confined to their isolated cages, collaborative robots are designed to interact safely with their human counterparts.
Notable examples of this transformative technology can be found already in the automotive industry. Companies like Nissan and Audi have embraced cobots on their assembly lines. These robots assist human workers in tasks that demand precision and strength, such as heavy lifting or intricate assembly. The result is not only increased efficiency but also a safer and more ergonomic working environment for human operators.
As cobots become more sophisticated and adaptable, we can expect to see them take on increasingly complex roles across various industries. New business models like robotics-as-a-subscription will allow smaller enterprises to reap the benefits of this technological breakthrough as well, by paying to use cobots on a subscription basis and therefore avoiding the high capital costs that are sometimes seen as a barrier to entry.
Predictive maintenance
The factories of tomorrow will not only produce goods with unprecedented efficiency but will also ensure that the machinery driving this production remains in peak condition. The use of predictive maintenance technologies, which harnesses the potential of the Industrial Internet of Things (IIoT), will revolutionize the approach to equipment upkeep.
By drawing upon the power of sensors, data analytics and machine learning, factories can predict when machinery is likely to fail and schedule maintenance proactively. This shift from reactive to proactive maintenance minimizes downtime, reduces costs and extends the life of equipment.
A great example of this technology in action can be found in the aviation industry. Rolls Royce, a leading aircraft engine manufacturer, uses advanced sensors to monitor the performance of its engines in real-time. This data is then analyzed to predict when components are likely to fail, allowing for targeting and timely maintenance.
Digital twins
Digital twinning is another revolutionary concept that promise to reshape the way factories operate. A digital twin is a virtual replica of a physical object or system, providing a real-time, dynamic representation of its counterpart. This technology is set to become a cornerstone of the factories of the future.
Siemens, a global powerhouse in electronics and electrical engineering, is at the forefront of embracing digital twins. In their factories, digital twins are used to simulate and optimize manufacturing processes before they are executed in the physical realm. This not only reduce the risk of errors but also allows for the fine-tuning of processes for maximum efficiency.
The application of digital twins extends beyond manufacturing processes to encompass entire production facilities. By creating a virtual model of the entire factory ecosystem, companies can identify bottlenecks, optimize workflows and make informed decisions to enhance overall efficiency.
Automated warehouses
Another key transformation that automation technologies are set to deliver in the next two decades is the automation of warehouses. This will revolutionize how goods are stored, retrieved and distributed.
Amazon is a trailblazer in the integration of automation and looking at their use of this technology gives an indication of what the future has in store. Their fulfilment centers possess an army of robotic systems that work seamlessly alongside human employees to fulfil orders with unmatched speed and precision. These robots, guided by sophisticated algorithms, navigate vast storage spaces, fetching products and delivering them to human workers for packaging. This collaborative approach streamlines the order fulfilment process, reduces errors, and significantly accelerates delivery times.
The factories of the future are likely to incorporate similar automated warehousing systems to enhance overall efficiency. The integration of robots, AI and advanced logistics management will not only optimize inventory handling but also pave the way for lights-out manufacturing — a scenario where factories operate autonomously 24-7.
Automated visual inspection
One of the most profound shifts we can expect to see in factories of the future is the widespread adoption of automated visual inspection. Enabled by advanced machine learning algorithms, AI-guided visual inspection systems are set to replace human inspectors, marking a paradigm shift in quality control.
At QualiSense, we are already delivering the technology of tomorrow, in partnership with Johnson Electric, a global leader in electro-mechanical components. AI guided visual inspection systems can detect defects at the end of the production line at far greater speed and with far greater accuracy than human workers, improving efficiency and yield.
While earlier versions of this technology necessitated a tiresome process of training the model, advanced machine learning algorithms have automated the process. This allows the AI model to be trained on fewer images and to prompt the quality manager for feedback and optimization. In future, we expect these systems to be implemented at every stage of the production process, not simply the end of the production line, and at the same time they will rapidly adapt to changes in production.
The application of AI and robotics to industrial and manufacturing operations will accelerate over the next two decades. It might be possible that these technologies are accompanied by other, as yet unimagined, technological breakthroughs. However, even if we simply project into the future the major technology trends of today we see a vastly transformed manufacturing landscape. The amount of data generated by advanced sensors will play an instrumental role in the transformation of manufacturing. Using AI to facilitate the centralization of manufacturing data and extract usable insights from it will be key. Exploiting this data will allow companies to not only take preventative measures to improve production processes, but to actually feed these data-driven insights into the design process itself.
A key question is the role of the human worker in the process. All of the changes anticipated in this article logically presuppose the replacement of human workers with machines. In the factories of the future, some of the more traditional manufacturing jobs will be automated and a smaller number of human workers will operate in the role of overseers. This is especially true in the field of visual inspection, where AI looks certain to replace traditional manual inspectors in many industries.
QualiSense is an award-winning artificial intelligence start-up that is introducing AI visual inspection systems at some of the world’s largest parts suppliers. To find out more, visit https://qualisense.ai
Comments (0)
This post does not have any comments. Be the first to leave a comment below.
Featured Product
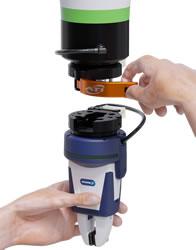