The absence of required machine safeguarding remains a perennial member of OSHAs Top 10 Most Cited Violations, and 2017 was no exception. It was named number eight on the list with a total of 1,933 violations.
Lack of Machine Guarding Again Named to OSHA'S Top 10 Most Cited Violations List
Contributed by | Rockford Systems
Reposted with permission from Rockford Systems:
Every year around this time, the awards season kicks off with the Emmys, Golden Globes and the grand daddy of them all, the Oscars, eagerly announcing their lists of nominations. At the same time — and on a far more somber note — another roll call is issued, this one from the Occupational Safety & Health Administration (OSHA). Unlike Hollywood’s awards celebrations, however, no one wants to be nominated for OSHA’s Top Ten Most Cited Violations list, let alone take home the top prize.
OSHA revealed its 2017 Top 10 list at the National Safety Congress & Expo in the Indiana Convention Center. The top ten are:
1. Fall Protection – (1926.501): 6,072 violations
2. Hazard Communication (1910.1200): 4,176 violations
3. Scaffolding (1926.451): 3,288 violations
4. Respiratory Protection (1910.134): 3,097 violations
5. Lockout/Tagout (1910.147): 2,877 violations
6. Ladders (1926.1053): 2,241 violations
7. Powered Industrial Trucks (1910.178): 2,162 violations
8. Machine Guarding (1910.212): 1,933 violations
9. Fall Protection – Training Requirements: 1,523 violations
10. Electrical – Wiring Methods (1910.305): 1,405 violations
While reviewing the list, it is important to remain aware that the Federal Occupational Safety & Health Administration (OSHA) is a small agency. When tallied up to include its state partners, OSHA only has 2,100 inspectors who responsible for the health and safety of 130 million American workers, employed at more than 8 million work sites. This translates to about one compliance officer for every 59,000 workers. As a result, some serious injuries are not reported and thousands of potential violations go without citation or fines. In fact, numerous studies have shown that government counts of occupational injury are underestimated by as much as 50 percent. Employers are required to record all injuries meeting the OSHA’s ‘recordable injury’ criteria (except minor first-aid cases) on the OSHA 300 Log, and those meeting the ‘reportable’ criteria (e.g., hospitalizations or deaths), are to be reported to OSHA immediately, or within 24 hours of occurrence, as per the criteria defined in 29 CFR 1904. But it doesn’t mean all of them do.
MACHINE (UN)SAFEGUARDING IN TOP 10 MOST CITED VIOLATIONS
The absence of required machine safeguarding remains a perennial member of OSHA’s Top 10 Most Cited Violations, and 2017 was no exception. It was named number eight on the list with a total of 1,933 violations. These violations refer to OSHA 1910.212 for failing to have machines and equipment adequately guarded. Any machine part, function, or process that might cause injury should be safeguarded. When the operation of a machine may result in a contact injury to the operator or others in the area, the hazard should be removed or controlled.
A lack of machine safeguarding also held the dubious distinction of making the list of OSHA’s ten largest monetary penalties for the year — not once but four times. In fact, the largest proposed monetary penalty, a staggering $2.6 million (USD), arose from an incident where a worker was crushed to death while clearing a sensor fault in a robotic conveyor belt. OSHA alleges that the company failed to use energy control procedures to prevent robotic machinery from starting during maintenance. The manufacturer also was cited for exposing employees to crushing and amputation hazards as a result of improper machine guarding, plus failing to provide safety locks to isolate hazardous energy.
Despite these headline fines, the repercussions for employers putting workers in harm’s way remain small under the 1970 Occupational Safety and Health Act. The average federal fine for a serious workplace safety violation was $2,402 in fiscal year 2016, according to the most recent report by the AFL-CIO. And the median penalty for killing a worker was $6,500.
According to the most recent Bureau of Labor Statistics data, manufacturing plants reported approximately 2,000 accidents that led to workers suffering crushed fingers or hands, or had a limb amputated in machine-related accidents. The rate of amputations in manufacturing was more than twice as much (1.7 per 10,000 full-time employees) as that of all private industry (0.7). The bulk of these accidents occurred while removing jammed objects from a machine, cleaning or repairing the machine, or performing basic maintenance. These injuries were all largely preventable by following basic machine safeguarding precautions. Rockford Systems is committed to helping organizations reduce injuries and fatalities due to a lack of or non-compliant machine safeguarding. By creating a culture of safety in the workplace, Rockford Systems can help plant managers significantly reduce the number of on-the-job injuries and fatalities that occur annually, plus guard against hefty fines, lost production and increased insurance premiums.
Which leads to the question… “Where do we begin?”
TRAINING AND EDUCATION
Ignorantia juris non excusat (“ignorance of the law excuses not”). Recognizing that education is key to safety, Rockford Systems has offered its Machine Safeguarding Seminars for more than two decades. Thousands of safety professionals have attended the seminars from industries as diverse as aerospace and metal fabrication, to government and insurance.
Held ten times a year at our Rockford, Illinois headquarters, the 2.5 day seminars address key topics in safeguarding with a focus on OSHA 29 CFR and ANSI B-11 standards as they relate to specific machine applications and production requirements. Safeguarding equipment, both old and new, is not only explained in depth in the classroom, but demonstrated under power on the shop floor. Most of these machines are equipped with more than one type of safeguarding product so that attendees can see how different guards and devices can be applied.
Roger Harrison, Director of Training for Rockford Systems and an industrial safeguarding expert with over 25,000 hours of training experience, conducts the Machine Safeguarding Seminar.
ASSESSMENTS
If your organization is interested in safeguarding solutions, consider a Machine Risk Assessment or Machine Safeguarding Assessment as the critical first step in any machine guarding process as outlined in ANSI B11. Most assessments, but not all, follow the basic steps outlined below.
Step 1 – Provide Machine List
To get started, please provide Rockford Systems a list of all machines (manufacturer, model number, and machine description of each machine) to be assessed. This machine list is needed to determine the estimated resource requirement for the onsite audit. Upon receipt of your machine list, an Assessment Proposal will be provided, generally within 24 hours of receipt. Please email your machine list and any machine photos (optional) to sheryl.broers@rockfordsystems.com.
Step 2 – Schedule Onsite Visit
During the assessment, a machine safeguarding specialist will visit your site and conduct a complete audit of all machines identified on the list and evaluate their compliance in five guarding areas (Safeguards, Controls, Disconnects, Starters, and Covers). The assessment is based on OSHA 1910.212 General Requirements (a)(1), ANSI B11 Safety Standards for Metalworking, ANSI/RIA R15.06-2012 Safety Standards for Industrial Robots, and NFPA 79. If Rockford Systems, LLC has additional specific safeguarding requirements above and beyond OSHA 1910.212 and ANSI B11, please provide them before the site visit and we will incorporate them into the assessment.
Also, during the assessment, we may request copies of electrical, pneumatic and/or hydraulic schematics and operator manuals for specific machines. This information is needed for our Engineering Department to review the control circuit for electrical compatibility of equipment being offered, to verify control reliability of the control circuit, to determine interfacing requirements of suggested equipment. If requested, this information would be needed before advancing to Step 3 below.
Step 3 – Receive Compliance Report and Safeguarding Project Proposal
Upon completion of the assessment, a Compliance Report and Safeguarding Project Proposal will be provided to that identifies where each machine is in, or not in, compliance with the above stated regulations and standards. Where not in compliance, we will suggest guarding solutions to bring the machines into compliance, along with associated costs and timeframes.
We look forward to assisting your organization with its safeguarding needs. A team member will call you within 24 hours to further discuss your needs and applications. We are here to help businesses large and small address machine safety challenges and to remove the burden of managing the growing legal complexity of OSHA, ANSI and NFPA requirements from simple turnkey solutions to build-to-spec customized solutions.
Please contact sheryl.broers@rockfordsystems.com or call 1-815-874-3648 (direct) to get started on an assessment today.
PRODUCTS
If you are looking for Machine Safeguarding Products, please visit our PRODUCTS page that offers over 10,000 safeguarding solutions for drill presses, grinders, lathes, milling machines, press brakes, power presses, radial arm drills, riveters and welders, robots, sanders, saws and more.
RETURN ON INVESTMENT
Not sure if the investment in machine safeguarding provides a return on the investment (ROI), it absolutely does and we can help you calculate it. Please read our detailed blog post on this topic.
The content & opinions in this article are the author’s and do not necessarily represent the views of RoboticsTomorrow
Comments (1)
Featured Product
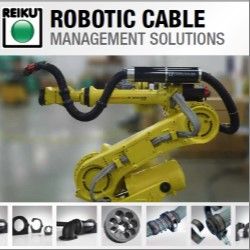